In 2019, the University of Maine in the United States stunned the world when it unveiled a boat produced with its 3D printer. It wasn’t a toy boat, either. Measuring 7.6 meters/25 feet, it weighed 2,268 kilograms/5,000 pounds. The boat, named 3Dirigo, took about 72 hours to produce, far less time than the many months traditional boatbuilding methods require. The printer itself is notable, the world’s largest 3D printer, capable of making objects whose dimensions are as large as 30.5 meters by 6.1 meters by 3 meters (100 feet by 20 feet by 10 feet, respectively). No wonder, then, that the university earned three Guiness Book of World Records, including for the world’s largest solid 3D printed item.
Although society is not yet at the point where superyachts can be 3D printed, the yachting industry and the larger recreational marine industry have definitely been using the technology for several years. Here’s a look at some of the leaders in the field, and what they’re doing.
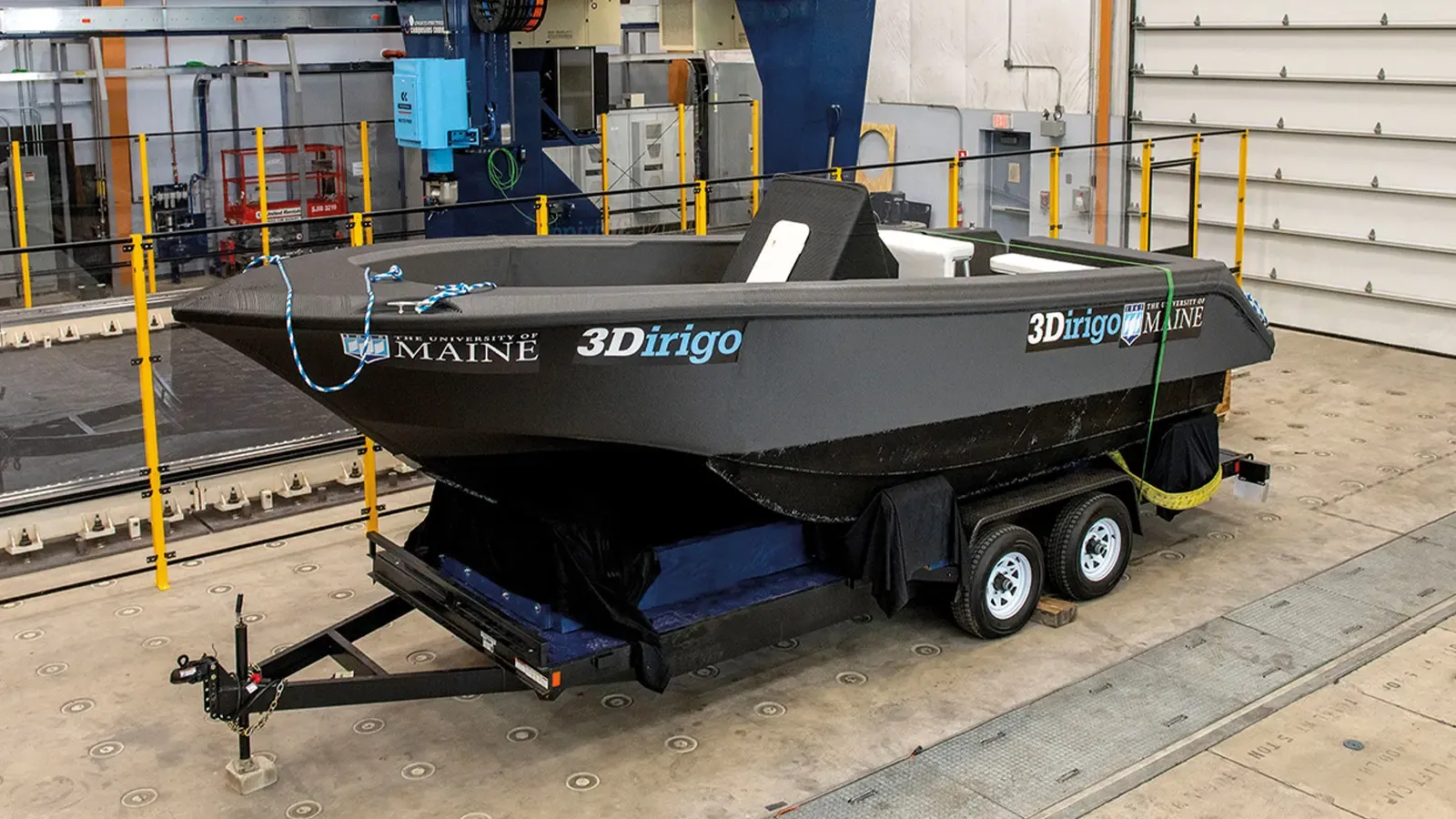
Hodgon Tenders
Hodgdon Tenders, a division of Hodgdon Yachts, one of the oldest superyacht companies in the world, has been using 3D printing for a number of years. Primarily, it’s manufacturing components like hull side doors, gloveboxes, and some stainless steel pieces. Light fixtures, door latches, and actuator mounting brackets are among the metal pieces it 3D prints, in fact. The components are for its popular limo, open, beachlander, and all-electric tenders from 6.5 meters to upwards of 12 meters. Additionally, Hodgdon Tenders employs 3D printing to help create the molds for some other small parts.
Notably, Hodgdon Tenders is in Maine in the United States, about two hours by car from the University of Maine’s 3D printer. The shipyard and the university collaborate on a few projects.
Paradoxal Surfboards
Surfers are some of the most eco-conscious people around, so it may come as no surprise that a surfboard company has begun manufacturing its boards from natural products through 3D printing. Paradoxal Surfboards uses algae (collected straight from beaches) and bio-sourced fibers instead of the long-traditional polystyrene foam. The 3D manufacturing process actually makes the surfboards stronger, too, especially in areas subject to a lot of stress and bending, because it helps create lattice-like structures with empty cavities. This, the company discovered, helps preserve the surfboards from dents. Overall, 3D printing’s precision helps reduce waste as well.
Fun fact: The founder of Paradoxal Surfboards was inspired to use algae after watching several lectures about biomimicry, which is the process of emulating nature’s solutions to design and create manmade things. Upon seeing a microscopic-level photo of a particular algae, he realized it had the same shape as a surfboard.
Silverlining furniture
Silverlining Furniture designs exquisite custom credenzas, dining tables, chairs, outdoor furniture, and more for some of the most elegant superyachts afloat. It also makes everything it designs, at its own workshop in England. Since the company’s founding in the 1980s, it’s been experimenting with manufacturing techniques and materials. Naturally, 3D printing is among those techniques. Recently, Silverlining Furniture began experimenting with 3D printed alternatives to ceramics. Dating back to the ancient Greeks, artisans have thrown pottery, meaning used their hands to shape clay on a spinning wheel. Advances in 3D printing, though, allow Silverlining to use not only the same materials that have long been used for porcelain, but also terracotta, stoneware, and even concrete. The process affords the team the ability to create shapes that simply cannot be made through any other method, plus it’s quicker and more cost effective.
Tanaruz boats
Around the turn of the millennium, a few Dutch nationals were so convinced that 3D printing would make boatbuilding more efficient and therefore more affordable for the general public that they created a boat-manufacturing company. Tanaruz Boats 3D printed its first boat in 2001, and is currently striving to scale up its production. In the meantime, it uses one of Europe’s largest 3D printers for latest design, the 6.5-metre/21-foot Ozare 6.5. The boat is ideal for cruising with up to eight people on inland waters like lakes, rivers, and canals. Interested customers include fellow residents of The Netherlands as well as buyers as far away as Australia. Additionally worth noting, Tanaruz Boats employs a recycled plastic and fiberglass compound purposely made for large-scale boat printing. Manufacturing each boat as one piece makes them more recyclable, too, equally important to the company.
We’re not yet at the point where we can have abundant full-scale tenders, watertoys, and even yachts produced by 3D printers. But, the time and cost savings currently are enough to make forward-thinking companies eager to implement the technology in the future. Considering how quickly technology advances, that future may not be as far away as we think.
By Diane M. Byrne
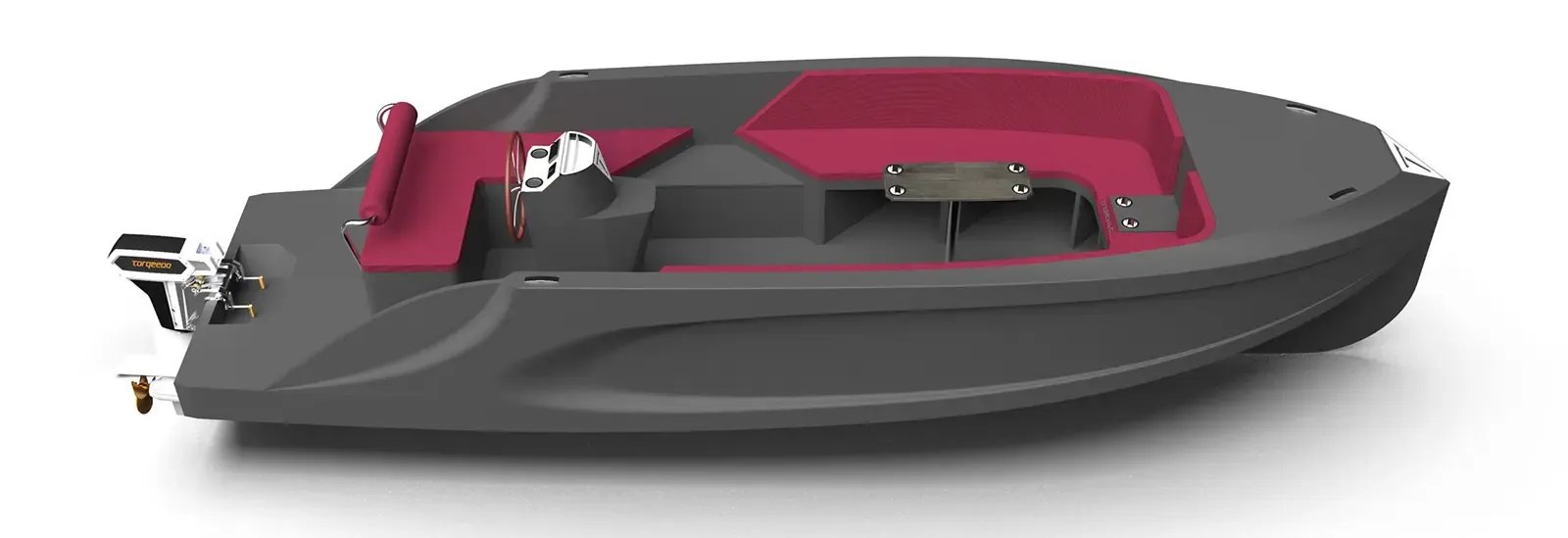